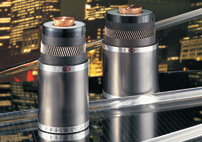
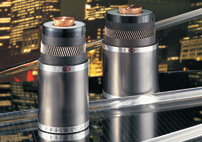
EXTRA HIGH VOLTAGE XLPE CABLE
Since its inception in 1959, XLPE cable has become the mainstream of power cable due to its excellent electrical and physical properties, easier installation, operation and maintenance than oil-filled cable etc.. In recent years, but also because of the considerable improvement of materials and manufacturing technology, the quality of XLPE has been significantly improved. This made its application field has also been rapidly expanded.
Since 1967, PEWC has successfully developed the 15kV cable first in Taiwan for over 40 years. During this period, we continue developing materials, manufacturing, testing and other technical equipment to improve quality. For instance, we have a solid base on the field of manufacturing, testing and installation of 161kV Extra High Voltage Cable. Nowadays, we also promote to develop 345kV cable manufacturing.
QUALITY REQUIREMENT OF EXTRA HIGH VOLTAGE XLPE CABLE
Because of its large capacity, high system voltage and high electric field strength, the requirements of quality and service life for extra high voltage cable are generally higher than those of high voltage cable. The main quality requirements are as follows:
- Uniform Insulation
The insulation material of XLPE cable is generally a mixture of polyethylene, cross-linking agent, aging agent, oxidizing agent and these materials should be uniformly blended and dispersed to uniformize the quality performance of XLPE insulation, Otherwise it will seriously affect the aging characteristics and water absorption. - Smooth Interface between Inner & Outer Semi-conducting Layer and Insulation and shall be firmly Bonded
Because of high electric field strength, interface roughness or insufficient adhesion at the interface produces steep electric field in the insulation and existence of cavity which will cause electric discharge leading to voltage breakdown which are seriously affect the service life of XLPE cable. - Avoid voids, moisture and contaminant
Voids, moisture and contaminant in XLPE insulation are always considered to cause electric discharge in high electric field and treeing phenomenon which will seriously affect the service life of XLPE cable.
Essentials of Manufacturing for Extra High Voltage XLPE Cable
- In order to avoid partial over-potential, conductors need to minimize the gap between wires, so most of the conductors are circular compacted stranded. Large cross-section conductor is made in form of Milliken segmental construction so as to avoid the skin effect which will reduce transmission efficiency.
- In order to avoid the defect like voids, moisture, contaminant and protrusion of semi-conducting layer into the XLPE insulation etc.. The following measures must be taken during manufacturing :
ACarefully choose good quality control materials. Besides, clean and closed indoor materials feeding system with dust-free device is required during extrusion.BGood Designed extrusion equipment, precise temperature control and cooling system are required to achieve uniform extrusion so as to avoid scorch and protrusion of semi-conducting layer.CThe conductor screen, XLPE insulation and the insulation screen shall be extruded in one common crosshead to ensure that the interface between screens and insulation are smooth and prevent mix with foreign materials and gap produced.DDry curing and cooling process to reduce the formation of voids and moisture.EControl the extrusion and curing process by computer calculation and strict quality control to ensure quality. - In order to achieve ground potential for insulation shield, copper tapes, copper wires or other suitable materials having good conductivity shall be applied to carry fault current in case of system fault.
- In order to provide mechanical protection, material having good abrasion resistance, oil resistance, acid/alkali resistance and also flame resistance shall be applied as cable outer-sheath. The outer sheath surface of cable shall be evenly coated with conducting graphite. Voltage test shall be applied after cable installation so as to confirm whether any damage to the cable.
CONSTRUCTION OF EXTRA HIGH VOLTAGE XLPE CABLE
- Conductor: Circular Compacted Stranded or Milliken Segmental (≥800mm²) Copper Conductor
- Conductor Shield: Extruded Semi-conducting XLPE compound.
- Insulation: Un-filled super-smooth XLPE
- Insulation Shield: Extruded bonded Semi-conducting XLPE compound.
- Metallic Shield: Copper Tape, Copper wires or metallic sheath.
- Water Proof Layer: Water swellable tape or laminated metal tape shall be applied
- Outer Sheath: PVC or PE surface coated with graphite
TEST ITEM OF EXTRA HIGH VOLTAGE CABLE
- Construction Check
- Physical Properties of Insulation & Outer-sheath
- Structural Stability Test
- Dimensional Stability Test
- Conductor Resistance Measurement
- Insulation Resistance Measurement
- A.C. Voltage Test
- D.C. Voltage Test
- Partial Discharge Measurement
- Capacitance & Power Factor
- Impulse Test
- Cyclic Aging Test
- Accelerated Water Treeing Test
161kV Single-core XLPE cable | 69kV Single-core XLPE cable |
---|---|
![]() |
![]() |
161kV Single-core XLPE cable datasheet![]() |
69kV Single-core XLPE cable datasheet![]() |